Do you fire incompetent workers?
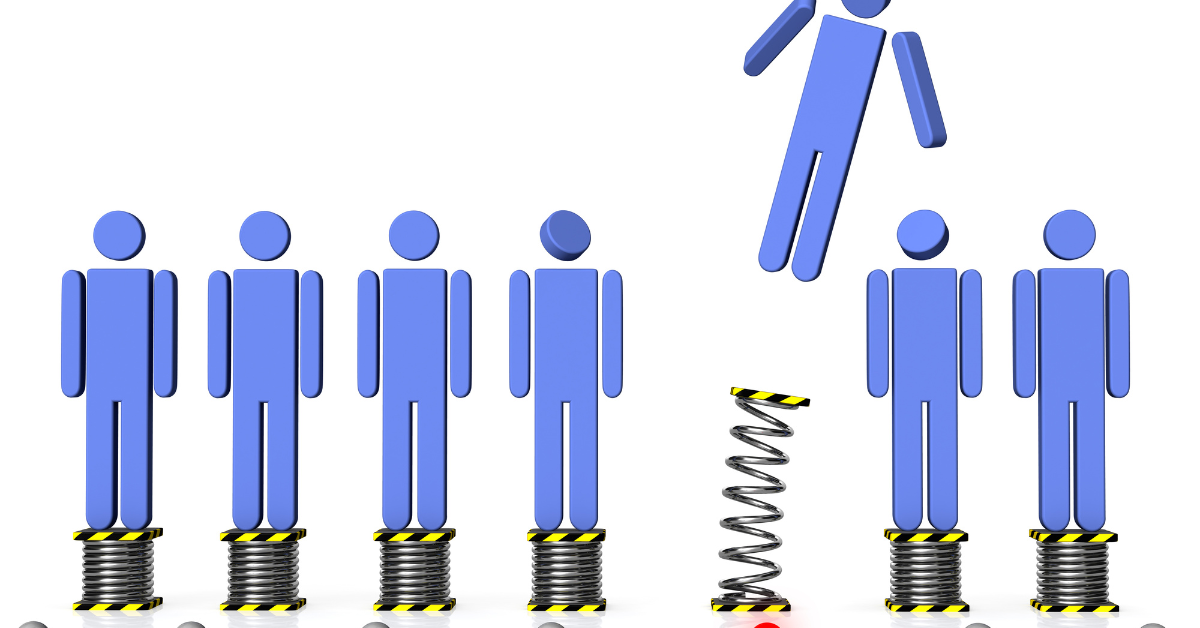
I attended an event last weekend, and someone I met there asked me what kind of work I do. I told him I was a TapRooT® Root Cause Analysis Instructor. He replied he was a retired manager at a manufacturing plant. He sighed heavily and continued, “I sure had to fire a lot of incompetent workers who got hurt at that plant or caused losses.”
This statement made me think (even though I tried to disconnect and NOT think about work that day). But … curiosity got the best of me. So, I smiled and asked him, “What kinds of things do ‘incompetent workers’ do to get fired?”

Incident #1: Machine inadvertently activated – worker injured
The first story he told me was about a worker who climbed into a piece of machinery to clean it, and it activated. He said the worker got injured “but could have died so he needed to be fired.”
I had to ask, “the worker needed to be fired because he could have died?” He explained that the worker was required to ensure the machinery was shut down and de-energized before cleaning it. The worker thought he had done so but didn’t do it right. I asked him if he knew anything about how the worker made a mistake like that, and he said either the worker was rushing through the procedure or totally disregarded it.
I asked him if the machine spontaneously turned on, and he said another worker activated it not knowing he was inside. So, I asked him how that worker did not know the other worker was in the machine, and he said something obstructed his view. And not only that, “another worker got fired for almost the same thing a few weeks later!”

Incident #2: Forklift crashes into skids – financial losses
The next story he told me was about a worker who noticed a spill on the plant floor and retrieved the wrong type of cleaner to clean it up. The solution he used made the floor very slick. Then a forklift came flying through the spill area and slid into some skids. The skids fell over, causing “thousands and thousands of dollars in losses so the worker who cleaned up the spill with the wrong solution was fired.”
I asked him how the spill happened in the first place, and he shrugged and said he didn’t think they ever looked into that. I also asked him if he knew how the worker decided to use the cleaner he used, and he said the worker was “probably just trying to be helpful and grabbed something.”
I didn’t say too much beyond that except that in a TapRooT® Investigation, we would look at how we could improve the system instead of firing the worker. But … I’ve been thinking about these two incidents. I like solving puzzles, so I’m asking you to help me out.
What questions do you have?
In Incident #1, there was a mistake shutting down the machinery, and the manager felt it was because the worker did not use a procedure or rushed through the procedure.
I have a lot of questions about the procedure off the top of my head. Here are just a few:
- Was the procedure readily available to the worker?
- Is there some reason the worker may have followed the procedure incorrectly, for example, was it in checklist form for ease of use?
- Did anyone look at the procedure to see if the right one was used?
I also would want to talk to the worker who started up the machinery.
- Was there a procedure to start up the machinery?
- What was obstructing the second worker’s view from seeing the first worker?
- Were there any displays or alarms on the equipment that would indicate something was wrong?
I am also curious to know:
- Was “fire the employee” the only corrective action implemented before another worker got fired for the same type of scenario?
Can you think of any other questions you would ask about incident #1?

Incident #2 makes me uneasy as well. The worker was fired for using the wrong solution to clean up a spill and a forklift somehow entered into a very slick area, slid into some skids, and knocked them over.
I have more questions, including:
- How did the spill happen in the first place?
- What’s the process to isolate an area until it is cleaned and dried?
- Were the cleaning solutions labeled so it was clear which one should be used?
And about the forklift crash:
- What did the forklift operator know about the spill?
- Was the forklift operator fatigued or overwhelmed?
- Where were the skids located?
What else would you ask about incident #2?
Were “incompetent workers” the problem?
I left the conversation feeling like one worker was fired for making a mistake in a procedure and another was fired for trying to be helpful. I don’t think I would call either one of those workers “incompetent” based on that information.
And I wouldn’t call the manager incompetent either. I don’t have any information about what kind of message or pressure he was getting from upper management. I don’t know if he had been trained to conduct incident investigations or if he was just doing the best he could within his own knowledge. I don’t know how many people he was managing at once but he seemed like a caring person who was frustrated with workers being hired who he perceived lacked important skills.
The incidents above seem to point to lots of system problems including inadequate training, poor procedures, lack of work direction, and hazardous work environments. If I was trying to do those jobs under these circumstances, I’d probably be labeled “incompetent” as well!

Do you know how I would think of more information to collect about both of these incidents to make sure I didn’t miss anything?
I’d do a formal TapRooT® Investigation to ensure I collected the information I needed. THANK GOODNESS the TapRooT® System is a guided system created with the help of human factors experts, 30+ years of research, and expert-user input. There is no way I would remember (or have the knowledge in my memory to retrieve) all the information I should be collecting every single time with so many different circumstances that occur. Just when you think you’ve seen it all, you haven’t. Can you relate?
Do you want tools to use in your investigation that will help you ask the right questions to find and fix root causes that are driving mistakes at your facility? In our 2-Day TapRooT® Root Cause Analysis Training and 3-Day VIRTUAL TapRooT® Root Cause Analysis Training, you receive all the tools you need to do an effective incident investigation from start to finish.
Firing workers doesn’t fix system problems. Learn our system to ask the right questions, and you’ll find fewer “incompetent workers” to fire at your facility.