7 Things to Consider to Advance Your Root Cause Analysis Skills
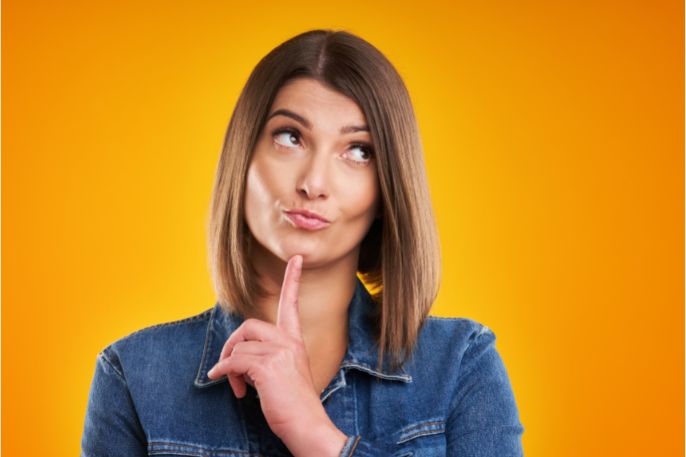
Advance Your Root Cause Analysis Skills
If you aren’t a TapRooT® user, you need to learn about incident investigation, root cause analysis fundamentals, and advanced root cause analysis. See our courses HERE.
But what if you already have taken a 2-Day TapRooT® Root Cause Analysis Course or a 3-Day Virtual Root Cause Analysis Course? There are seven more things you should be considering to advance your root cause analysis skills.
Seven Things TapRooT® Users Should Consider
Here are the seven things you should be considering…
- 5-Day TapRooT® Training
- Equifactor® Course
- Evidence Collection
- Stopping Human Error
- Spreading Use of TapRooT® Across Your Company
- Bringing an Improvement Team to the 2023 Global TapRooT® Summit
- Developing Your Roadmap to Success
If you are interested in any of these topics, read the applicable section below for more info!
1. 5-Day TapRooT® Advanced Root Cause Analysis Team Leader Training
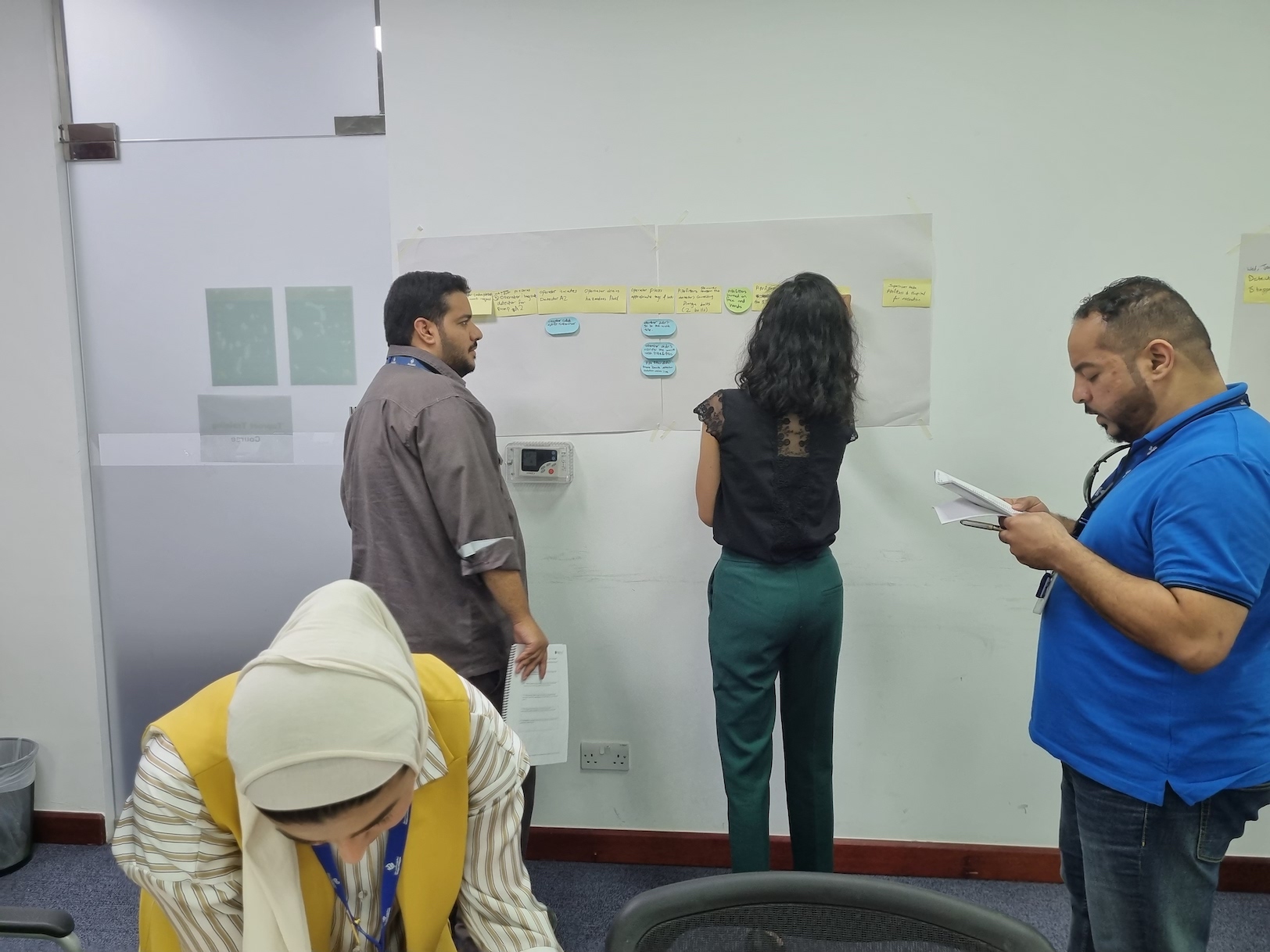
There is more to learn than the topics in the 2-Day/3-Day TapRooT® Courses. That’s why we created the 5-Day TapRooT® Advanced Root Cause Analysis Team Leader Course.
The 2-Day/3-Day TapRooT® Courses teach the essential techniques for low to moderate risk incident root cause analysis. But the 5-Day TapRooT® Course teaches the essentials plus the knowledge/skills you need to succeed when performing a major investigation. CLICK HERE for the complete course outline.
Did you know that if you have already completed a 2-Day or 3-Day TapRooT® Course, you can get a $500 DISCOUNT OFF the price of a 5-Day TapRooT® Course? Contact us at 865-539-2139 or info@taproot.com to get your discount coupon code.
2. Equifactor® Course
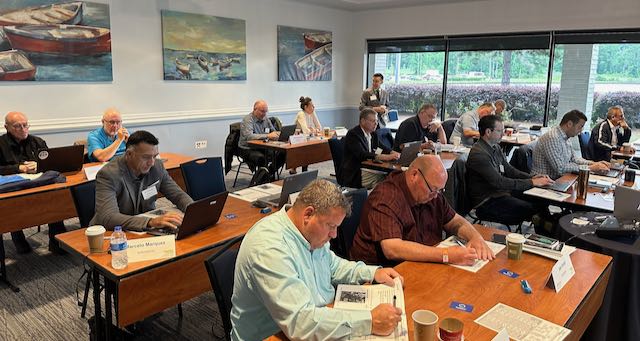
If you have already attended a 2-Day or 3-Day TapRooT® Course and would like to know more about troubleshooting equipment failures, then the 2-Day Equifactor® Equipment Troubleshooting & TapRooT® RCA Course.
What do you learn in this course? The topics include:
- Equifactor® Troubleshooting Tables
- Change Analysis
- Analyzing what happened with a SnapCharT® Diagram
- FailureModes/Failure Agents
- FRETT
You will also practice your new skills by participating in realistic team exercises. Plus, you will learn how equipment troubleshooting fits into the TapRooT® System.
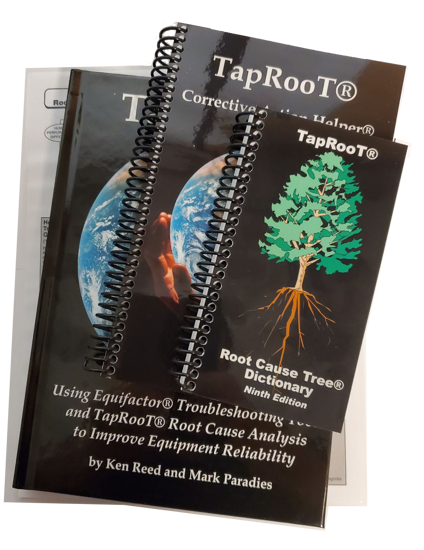
Root Cause Analysis to Improve Equipment Reliability
With the course, you get a copy of the book Using Equifactor® Troubleshooting Tools and TapRooT® Root Cause Analysis to Improve Equipment Reliability, a $129.95 value. You also get a 90-day free trial of the cloud-based TapRooT® Software that includes the Equifactor® Troubleshooting Module.
3. Evidence Collection
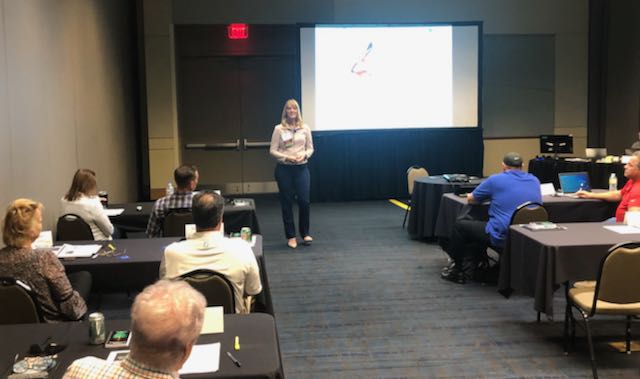
Would you like to learn more about evidence collection and interviewing? We have two options that might interest you…
- Take our training. Either a 1-Day on-site course or our 2-Day Course. See the agenda HERE.
- Take our self-guided online TapRooT® Evidence Collection & Investigative Interviewing Techniques course. The seven-module course will take you about three hours. Get more information HERE.
To register for either the live or the self-guided training, CLICK HERE.
4. Stopping Human Error
There are lots of folks who claim they teach you how to understand and analyze the causes of human errors and proactively improve human performance. However, nobody has done the research and development that Mark Paradies and Alex Paradies of System Improvements have to develop the 2-Day Stopping Human Error Course. CLICK HERE for more course info.
Watch the video above where Mark and Alex discuss the book Stopping Human Error.
You can’t afford to miss this course because stopping human error is essential to safety, environmental, maintenance, operational, and quality improvement.
For course dates, CLICK HERE.
5. Spreading Use of TapRooT® Across Your Company
Many companies use TapRooT® Root Cause Analysis across their corporation. They use TapRooT® RCA to improve:
- Safety/Process Safety
- Quality
- Equipment/Asset Reliability
- Operational Excellence
- Industrial Relation
Is your company using TapRooT® Root Cause analysis at all of its sites and across all departments? Perhaps you need to spread the word to other sites and departments. Have them attend one of our courses. They can get more information about our training HERE.
And they can read about TapRooT® user Success Stories in various industries and departments HERE.
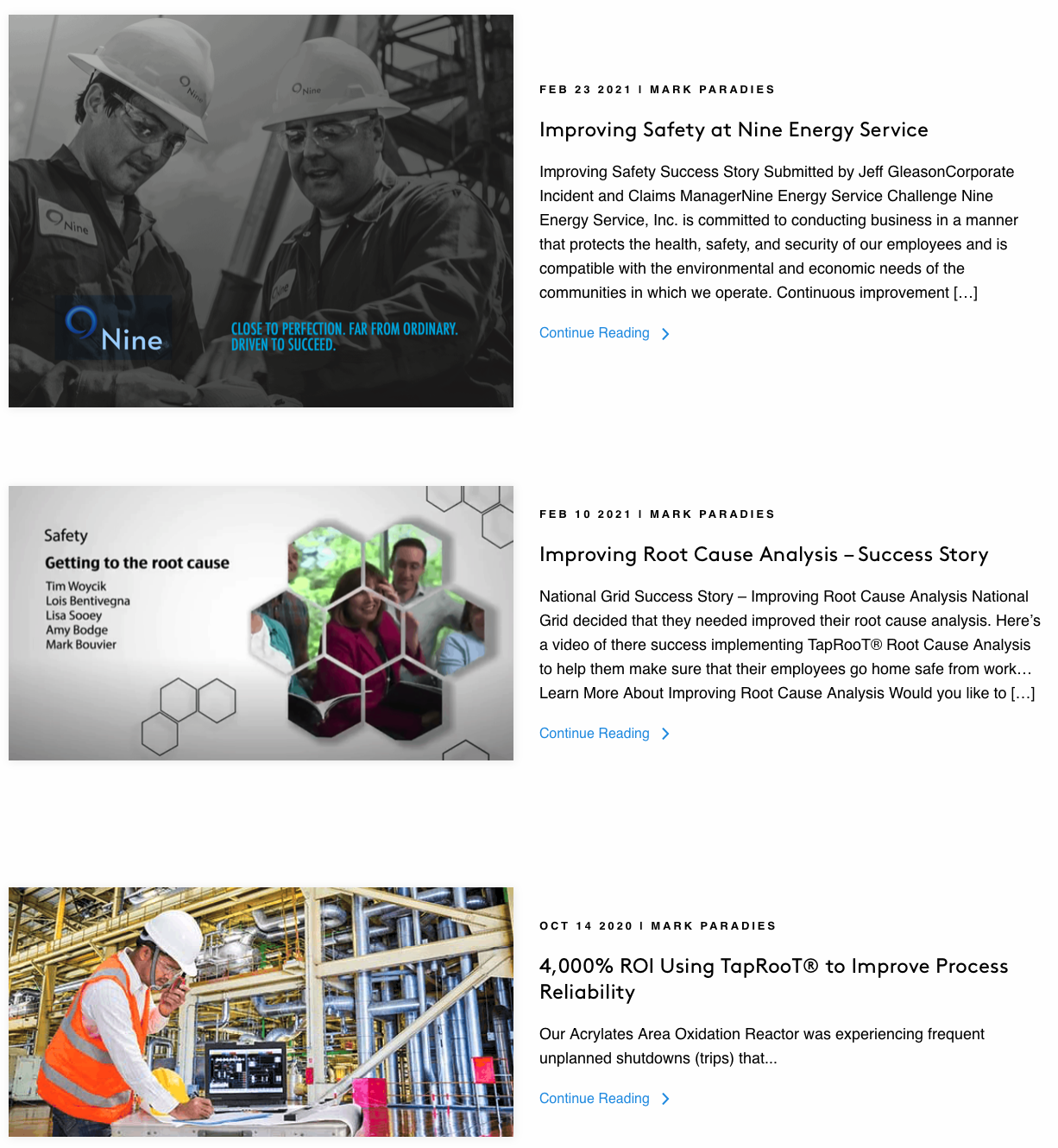
6. Bringing an Improvement Team to the 2025 Global TapRooT® Summit
Can a CEO alone make corporate wide improvement happen? NO! How about the corporate safety manager? NO! What about a maintenance manager or the quality manager? NO! Not even Lean/Six Sigma can make improvement happen all by itself.
Improvement requires a team effort.
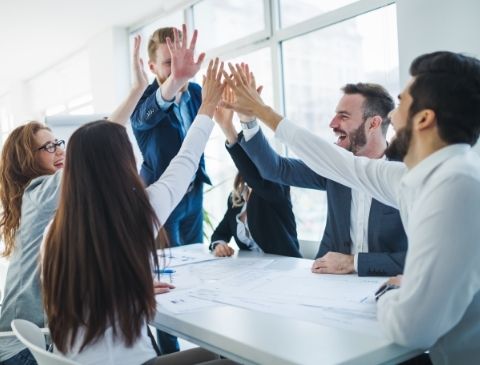
That’s why, if you are using TapRooT® RCA to improve performance at your company, you should bring an improvement team to the 2025 Global TapRooT® Summit.
Who should participate inthis improvement team? Here are some ideas…
- A senior management representative
- The corporate safety, quality, equipment reliability, and operational excellence managers
- Plant managers
- Site safety, quality, equipment reliability, operational excellence, human performance, and human relations managers.
- Union safety representatives
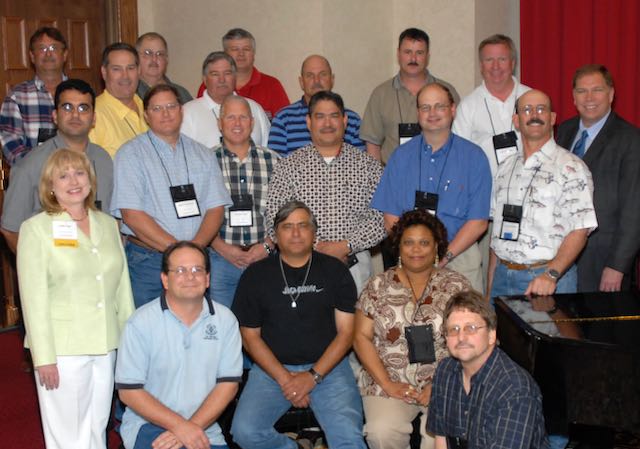
The biggest benefit of bringing a team to the 2025 Global TapRooT® Summit is that you won’t be alone going back to work to sell your great ideas and get them implemented. You will have a team to help you make progress happen.
Plus, when you sign up multiple team members at the same time, you will get a significant discount on the Summit and on Pre-Summit Courses…
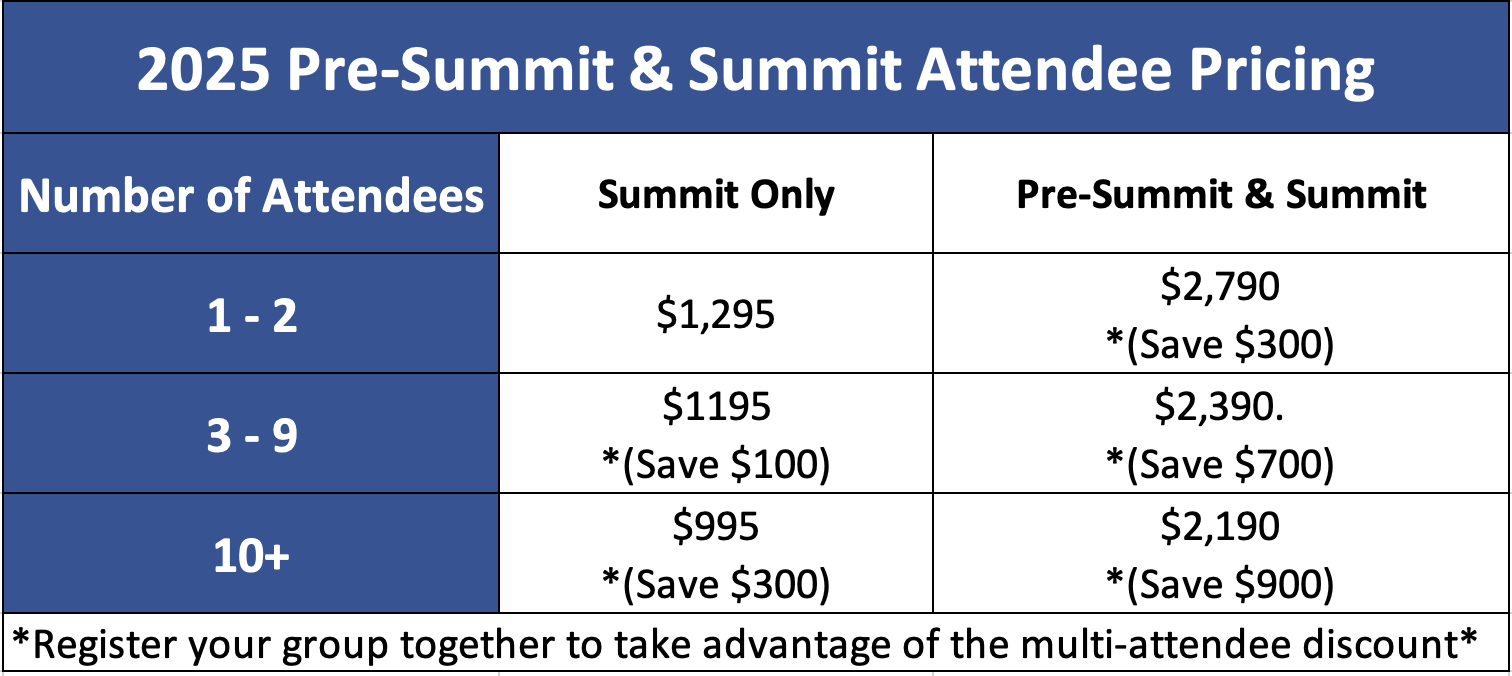
You save $9,000 when you bring 10 people to a Pre-Summit Course and the Summit.
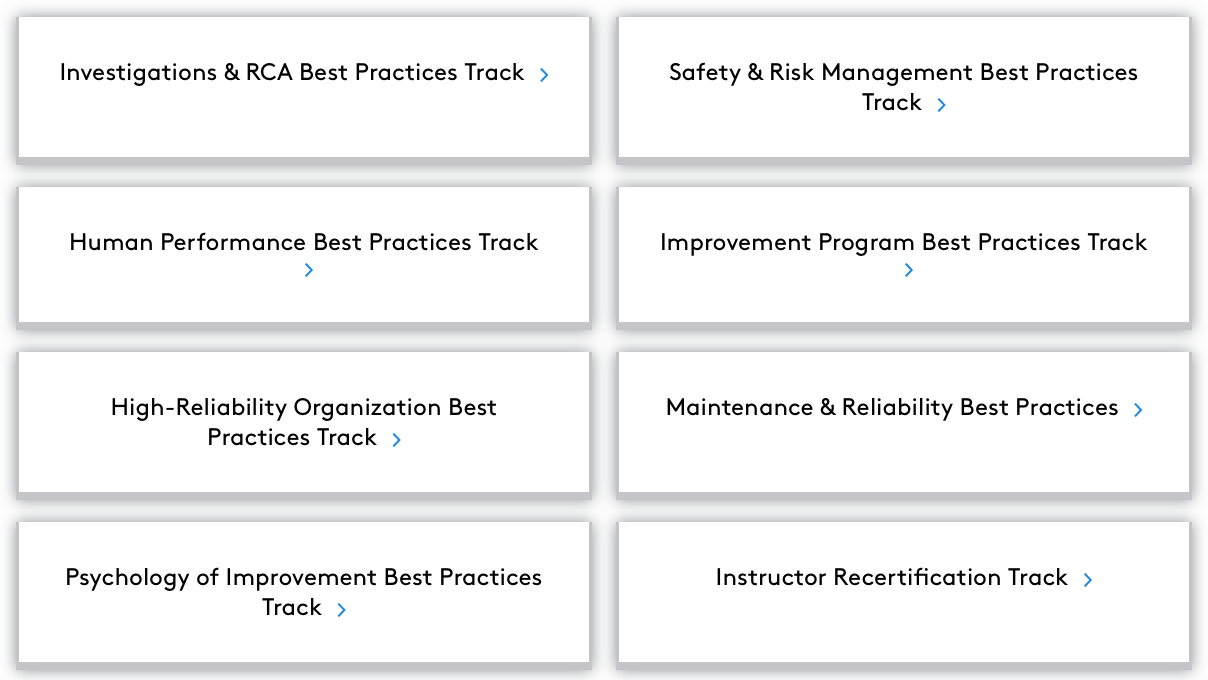
Everyone will be amazed by the learning and ideas they gain from the various Best Practice Tracks and the advanced knowledge and motivation they achieve from the Keynote Speakers.
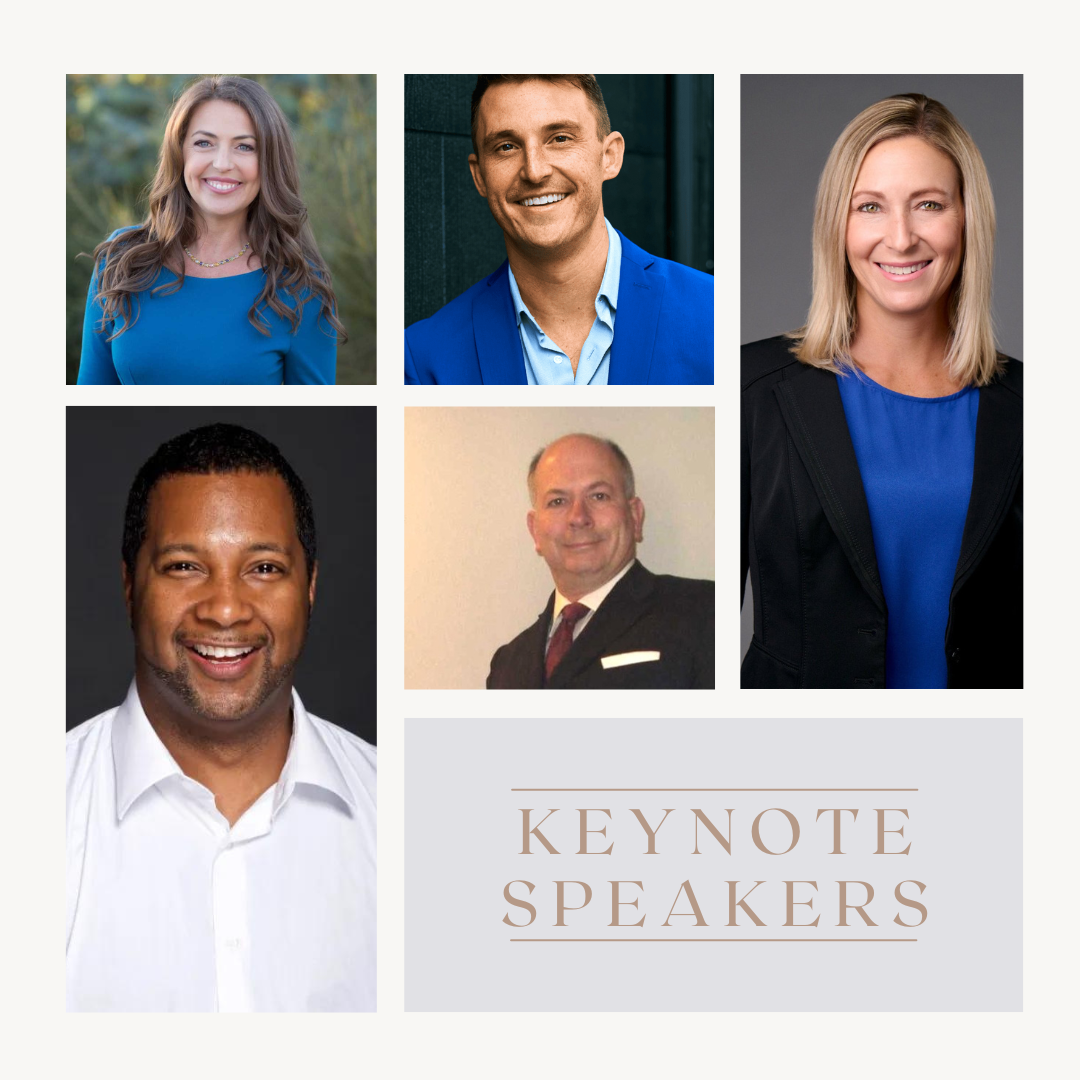
When and where is the 2025 Global TapRooT® Summit? October 1-3, 2025, at the Knoxville Convention Center in downtown Knoxville, Tennessee.
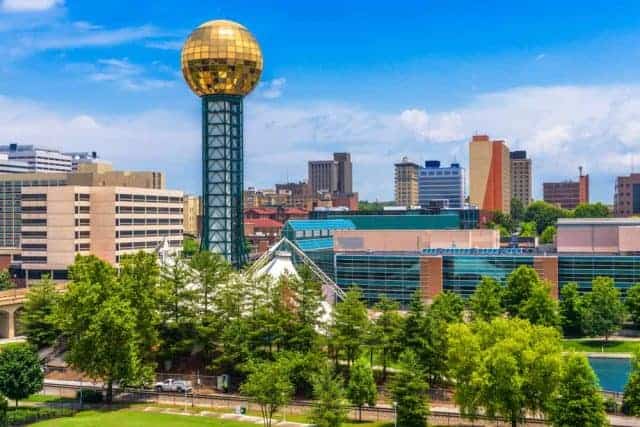
Don’t miss this opportunity to get your improvement team on the same track. REGISTER HERE.
7. Developing Your Roadmap to Success
Every company using TapRooT® Root Cause Analysis should have a Roadmap to Success. Your roadmap should include how your investigators will develop their skills and make their program better.
What is a Roadmap to Success?

It is one of the tools we use to ensure the successful implementation and continuous improvement of an improvement program. It helps you make and keep your improvement program world-class.
Here is a video about executive briefings and developing a roadmap to success…
We can help you develop your roadmap to success when you have an Executive Briefing (call 865-539-2139 to get your’s scheduled) or you can build one at the 2025 Global TapRooT® Summit.
Find out more about building a Roadmap to Success here…
Seven Great Ideas for TapRooT® Users!
For TapRooT® Users, that’s seven great ideas for achieving advanced root cause analysis. I think you should consider them all. At a minimum, you should select one or two of the best and get started improving your improvement initiative now.
If you would like to discuss any of these ideas with us, contact one of our Implementation Advisors at 865-539-2139 or by CLICKING HERE.

And for those who haven’t tried TapRooT® Root Cause Analysis yet … Get Started! Pick a Public TapRooT® Course HERE.